The line “Tallest, Strongest, Fastest” describing the just unveiled Statue of Unity (SoU) is no empty superlative speak. It’s an arithmetical fact.
At 182 meters, the SoU is the tallest statue ever built in all of human history. Capable of enduring windspeeds of over 180 kmph and earthquakes measuring up to 6.5 on the Richter Scale, it can withstand the most testing of challenges Mother Nature can throw at it. And finally, given how it was erected in just 33 months the SoU is by far the fastest built structure of its kind anywhere in the world.
Tallest, Strongest, Fastest. Built by L&T.
Rising on the strength of L&T’s world-class design-build prowess and project management capabilities, the SoU is a remarkable piece of engineering and a confluence of art and technology. But whereas much ink has already been spilled on the art and the engineering aspects of this 21st century marvel, the technology behind it remains largely uncovered. The digital tools that allowed designers and engineers to visualise the statue down to its last detail atop what was once a non-descript hillock, the geospatial technologies that helped the project team understand the topography of the riverbed and the hunk of earth surrounding Sadhu Bet, the Building Information Modeling (BIM) process which helped teams collaborate and orchestrate the massive task of planning, designing and constructing the statute and associated infrastructure, the list of technologies which didn’t quite make the papers is exhaustive to say the least.
In the early days of the project, much before engineering and design teams could get to work, for surveying the landscape where the SoU was to be erected Terrestrial LiDAR (Light Detection and Ranging) was used extensively to understand the topography of the place. A remote sensing method that uses light in the form of pulsed laser to measure coordinates, the LiDAR survey proved crucial as it helped the project team determine the exact contours of the rock on which the SoU was to stand.
The LiDAR instrument fires rapid pulses of laser at the surface, at a rate of approximately 150,000 pulses per second. A sensor on the instrument measures the time it takes for each pulse to bounce back. Since light moves at a constant speed, the instrument can calculate the distance between itself and the target with high precision. Done repeatedly in quick succession, terrestrial LiDAR can give highly detailed, complex maps of the surfaces it is applied on. Thanks to the LiDAR survey, the SoU engineering team was able to develop a 3D point cloud of the island and from it derive the specific contours of rock and incorporate those readings during the engineering and design stages.
Further, as part of a special geotechnical survey, a 3D profile of the Sadhu Bet island was developed to analyse its geological make-up below the surface. This was crucial since the island is located close to C6 fault lines and the project team wanted to ensure that there weren’t any major concerns regarding the seismic activity in the area and that the geology of the rock and the adjoining area was in fact stable for the project. Using a 3D model that gave a layered ‘cake slice’ like profile of entire hill, the team could study the earth accurately and adequately prepare the upcoming structure allaying any fears concerning SoU’s geological viability.
To learn about the surface below the water the team conducted Bathymetry study and Geospatial studies to map the topography of the riverbed. The information had a critical bearing on the M&VC's foundation. The exercise revealed that the site had large deposits of quarry material disposed from the Sardar Sarovar Dam construction. The Study helped in suitably developing the appropriate Engineering solution addressing these & ensuring life & safety.
The SoU stands on the downstream end of the Narmada river, a mere 3.5 kilometres from one of biggest dams in the world. This necessitated a careful study of the hydrodynamic pressures emanating from water flow under different conditions. These water pressures were derived digitally through simulation and models were created based on past data. The information not only proved crucial in designing a strong enough foundation for island which could withstand the water pressure of varying force but also the bridge connecting it to the mainland.
While geospatial technologies proved vital to the task of studying and preparing the SoU site and the neighbouring landscape, the construction of statue itself relied heavily on a number of digital tools. One of the core technologies crucial to the task was BIM. By driving design, cost and schedule optimization and integrated solutions through BIM, the SoU team was able to manage the task seamlessly. The BIM process allowed those working on the project to create and manage all the information, at every stage of project in a digital repository. Whether it was engineering drawings, 3D designs, planning and monitoring, material management, cost control, document management or clash resolution, the BIM process facilitated a seamless exchange between key stakeholders every step of the way.
BIM transformed SoU project management into a fully integrated effort and enabled designers and engineers to collaborate freely across geographies and share information about the project in workable formats.
One of the biggest challenges and potentially the most contentious issues relating to the project was the profile of the statue and here too digital technology was employed to arrive at a resolution. While the SoU is technically an artistic impression of Sardar Patel, given that he is a historical figure who lived as recently as 70 years ago, it was paramount that even with all the artistic liberties that the sculptor Ram Sutar could take, the statue resembled its famous subject as closely as possible. It was a task easier said than done since accounts of how Patel looked, stood and walked varied from person to person. After speaking to Patel’s family members, people who had seen him in person and historians, examining archival footage and trawling through thousands of pictures, two photographs of the former Deputy Prime Minister were chosen. Using the two pictures and a digital scan of one of his statues from the famous Somnath Temple, the project team arrived at a front and side profile for the SoU. The anthropometric features of the statue were further ratified after an Autodesk graphics team derived a 3D profile from this data.
Given the high-stakes nature of the project and the fact that Prime Minister Mr. Narendra Modi took a keen personal interest in the goings-on of the project, it was important to keep the client abreast of all the activities. For its part, the client was always keen on understanding the scale of what was being built. How the SoU would look from a certain distance or from a certain height? What would the interiors of the statue look like? How would it rise against the horizon with a sunset in the back? These were all real questions that the project team had to contend with. The answer for many of the queries came through Shristhi, L&T Construction’s captive 3D design studio.
At this Chennai-based facility design engineers were able to give clients a ‘virtual’ walk through every aspect of the SoU in all its glory. In fact, Prime Minster Modi too took at a virtual reality tour of the SoU site at a specially organised virtual walkthrough in New Delhi before signing off on the construction phase.
Of all the digital tools used in the construction of the SoU, perhaps the most important from a utility standpoint has been the use of QR Code and RFID. The SoU uses more than 6500 panels of varying shapes and sizes to make the exterior bronze cladding. To ensure that each of these panels were affixed without any errors at the project site, the SoU team created a 3D model of every single panel. This was done since with 2D drawings one could never truly understand all the unique characteristics of each panel. The project team therefore used QR Codes to connect the 3D images of each of the 6500+ panels and made them available to the people on their mobile devices. These QR codes were printed on the 2D drawings of each of the panel and upon scanning a QR code users would get an instant 3D view of the panel on their mobile phones. This brought tremendous fluidity to the operations and sped up the construction immeasurably.
RFID tagging brought further transparency in terms of tracking the movement of bronze panels, on-site assembly, installation and even repair. With RFID, personnel on site could track the panels in real-time using their mobile devices and find out whether the panels were at the yard and in what stage, pre-assembled or assembled? In case of panels already installed, RFID tagging makes it possible to seamlessly locate them on the structure and perform maintenance work if needed.
Statues are one of humanity’s oldest obsessions and time has done little to wither this most ancient of our desires. If anything, with time we have grown bolder and more ambitious dreaming up structures bigger and grander than before. The SoU serves as evidence of this. That said, what make the Statue of Unity stand out from all our previous endeavours – besides the jaw-dropping scale and the sheer magnitude of the effort it took to build – is a rare mix of engineering and digital ingenuity that L&T brought to the table. As only it could have.
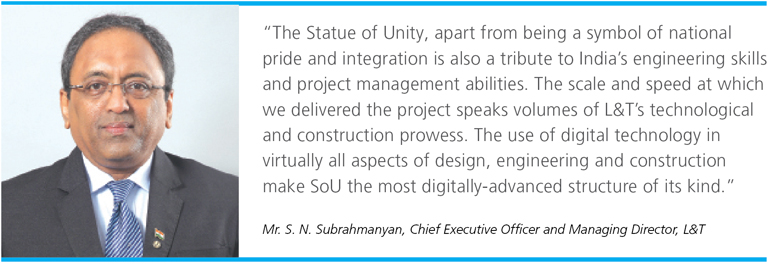